Steam Boiler Efficiency Enhancement
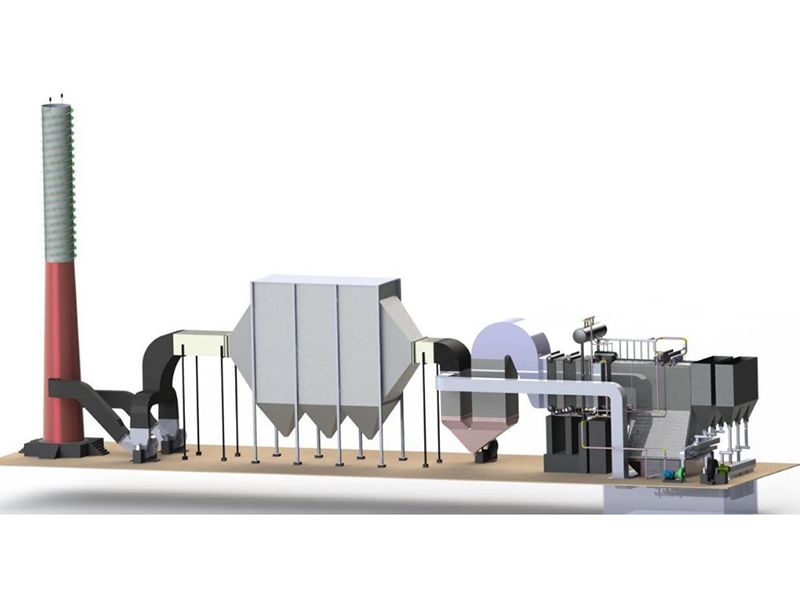
Why Core Axis For Industrial Steam Boiler Efficiency Enhancement?
- We provide customized solutions for steam boiler efficiency enhancements delivering maximum efficiency at lower fuel costs.
- Steam Boiler Efficiency Enhancements solutions are cost effective with low capital investment, with shorter payback period.
- Extensive experience with Steam Boiler Efficiency Enhancement projects for boilers operating on varied fuels.
- Strict quality control.
- Adherence to strict timelines through state-of-the-art time management schedules and processes.
- Our steam boiler retro fitting saves Operations and Maintenance costs for businesses.
Need For Steam Boiler Efficiency Enhancement.
- Investment Cost benefit: Instead of buying a new steam boiler system, enhancing efficiency of steam boiler is a more profitable preposition. Businesses can save on investment costs.
- Low Fuel Cost: Enhancing efficiency of a steam boiler, helps in lowering the overall fuel cost. Fuel costs are one of the major operating costs for an industrial unit.
- Better Fuel Utilization: One of the parameters that increases steam boiler’s efficiency is better fuel combustion. It helps in utilizing lesser fuel quantity for the process.
Factors That Contribute To Heat Losses.
- In order to improve boiler efficiency, it is important to ensure complete combustion of the fuel so that there is no unburnt
fuel in the residue. - Re-inject the unburnt carbon found in the discharge from the furnace for facilitating complete combustion of fuel.
- Utilize the high sensible heat of bottom ash from the boiler to preheat the air or water used in a boiler.
- Maintaining optimum ratio of fuel to air by keeping the excess air as low as possible can increase the furnace temperature and radiation heat leading to higher efficiency. Reducing excess air by 5% can increase boiler efficiency by 1%.
- Using moisture free fuel does away with the need of utilizing heat for drying up the moisture. This heat can be used for efficient fuel combustion instead.
- Dry flue gases leaving the boiler at high temperature account for major heat loss. Conduct regular boiler maintenance and remove the scale deposited on the heat transfer tubes for facilitating proper transfer of heat between flue gases and water.
- Continuous blowdown of water helps in keeping water impurities to optimum level but results in heat loss. So, keep a check on number of blowdowns per day and install a blowdown heat recovery system to preheat the water or air entering the boiler for reducing heat loss and improving boiler efficiency.
- Radiation and convection losses add to the heat loss. Although not measurable, these losses can be reduced by regular maintenance and insulation of the boiler.
- Condensate water, produced after transfer of heat from injected steam, has high temperature. It can be recovered using Condensate Recovery Module and reused to preheat water or air being fed into the boiler.
Industries We Serve
- Rice Mills
- Paper
- Sugar
- Textiles
- Food Processing
- Plywood
- Pharma
- Distilleries
- Brewery
- Chemicals
- Power
- Steel
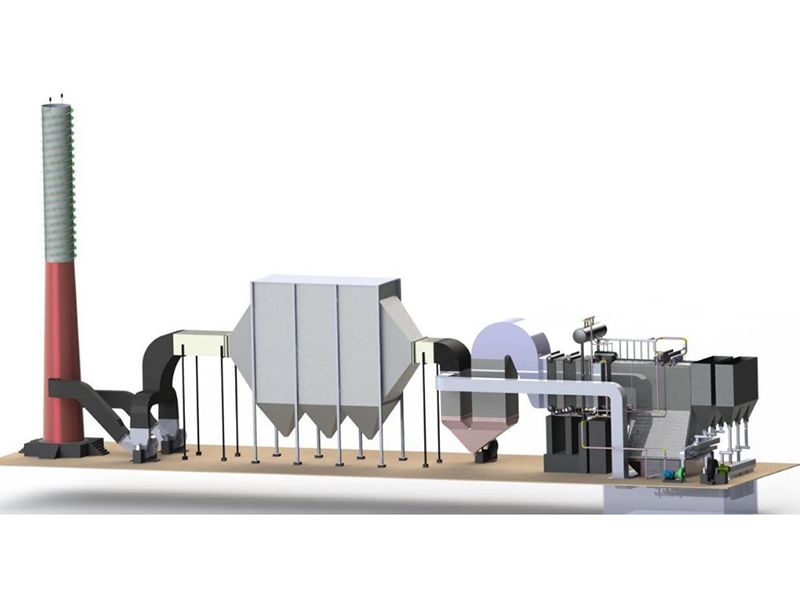